Resources
Resources
How Precision Milling Ensures Quality in Aerospace Manufacturing
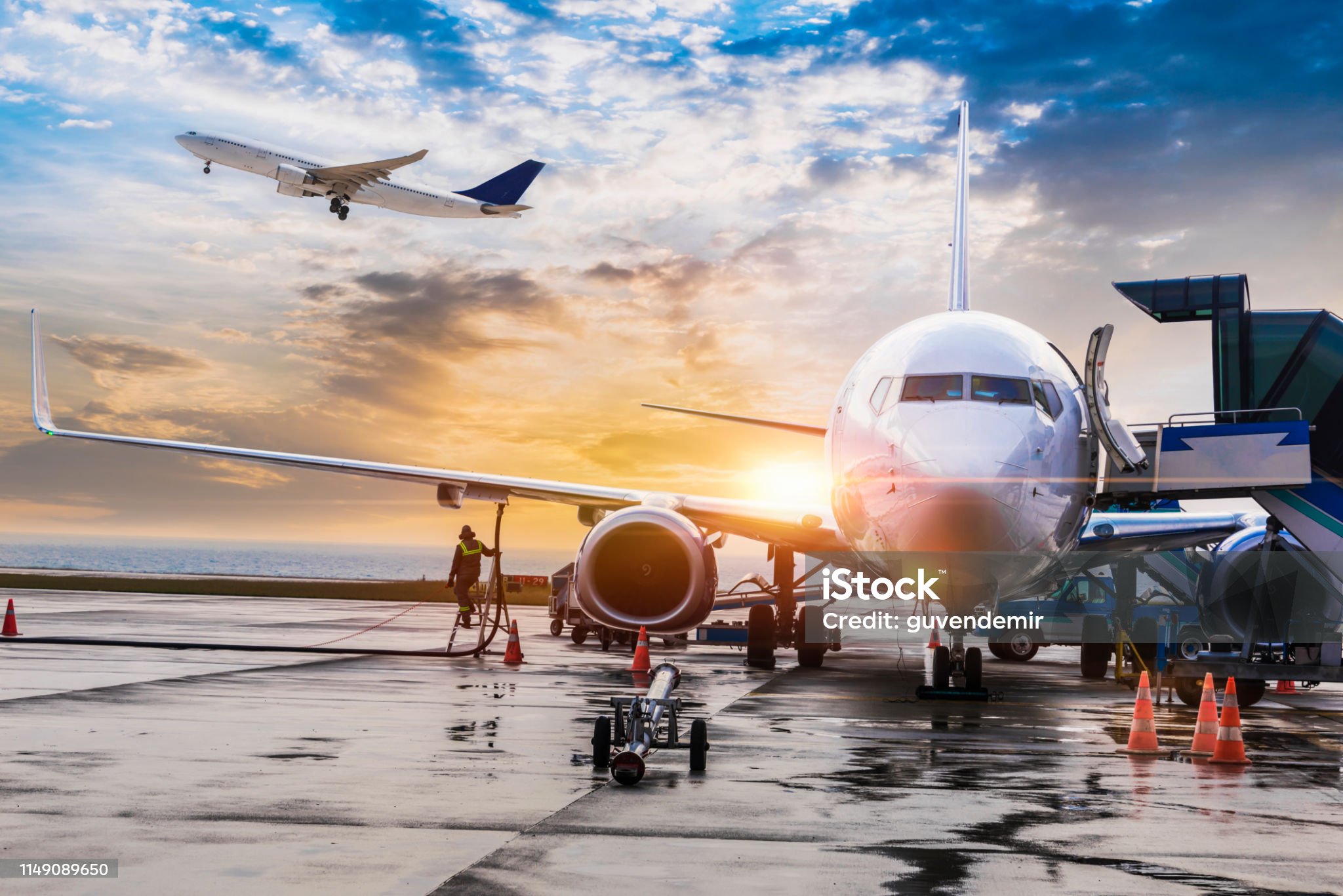
The aerospace industry sets some of the highest standards for precision and accuracy. Imagine assembling a complex machine like an aircraft, where thousands of parts need to fit together perfectly. Even the smallest miscalculation can result in severe issues. This is why precision milling is so essential—it’s the process that shapes and forms each part to meet exact specifications, ensuring they perform reliably in extreme conditions.
Why Precision is Everything in Aerospace
Inside a jet engine, things move fast. Turbine blades, shafts, and other components spin at thousands of revolutions per minute and endure temperatures that would melt ordinary metals. In such an environment, there’s no room for error. A minor misalignment or a slightly off dimension could lead to excess friction, vibration, or, in the worst-case scenario, catastrophic failure.
Precision milling makes it possible to create aerospace parts that meet these ultra-tight tolerances. Often, the required accuracy is down to a few microns—much smaller than a single grain of sand. This level of precision ensures that parts not only fit together perfectly but also withstand the stresses they’ll encounter in real-world conditions. In an industry where safety is paramount, this kind of exactness is non-negotiable.
Handling Complex Materials
Aerospace parts aren’t made from your typical metals. They’re often crafted from advanced materials like titanium, Inconel, and other heat-resistant alloys. These metals are chosen because they can handle high temperatures and intense stress, but they’re also notoriously difficult to work with. Regular cutting and shaping methods can cause warping or surface damage, compromising the final product.
Precision milling is designed to handle these challenges. Using high-speed cutting tools and advanced machinery, the milling process can shape tough materials while maintaining their integrity. It’s a delicate balance—too much force, and the part could deform; too little, and it won’t reach the desired specifications. Precision milling strikes that balance, producing parts that meet all requirements without compromising strength.
Different Milling Techniques for Different Needs
When people think of milling, they might imagine a simple cutting process. However, precision milling involves a variety of techniques, each tailored to a specific type of part or material. Here are a few of the most common techniques used in aerospace manufacturing:
- Vertical Milling: This is used to cut straight, vertical surfaces, making it perfect for components that need sharp edges and precise flat surfaces.
- Horizontal Milling: Horizontal milling is ideal for cutting slots and grooves into materials. It’s often used for more complex shapes, like engine components that require several interconnected cavities.
- 5-Axis Milling: This advanced method allows for machining intricate parts from multiple angles without repositioning the workpiece. It’s crucial for parts with complex geometries, like turbine blades or structural brackets.
- High-Speed Milling: As the name suggests, high-speed milling is about making precise cuts quickly. It’s perfect for tough-to-cut materials and reduces the risk of heat build-up that can damage sensitive metals.
Each technique has its own strengths, and choosing the right one depends on the specific needs of the part. That’s why experienced machinists use a combination of these methods to achieve the best results.
Maintaining Material Strength During the Process
One of the biggest concerns in aerospace manufacturing is making sure that the milling process doesn’t weaken the material. Milling creates a lot of heat and stress, which can alter the metal’s properties if not carefully managed. For example, high heat can cause micro-cracks or residual stress that lead to failures later on.
Precision milling addresses this issue by using controlled speeds, feeds, and cooling techniques. By keeping temperatures down and minimizing stress on the part, precision milling ensures that the material’s strength is maintained throughout the process. This careful approach is critical for producing parts that can withstand the rigors of aerospace applications without becoming weak or brittle.
Quality Assurance: Every Detail Matters
In aerospace, quality assurance isn’t just a step in the process—it’s embedded in every phase of production. Each component has to meet stringent requirements, from its dimensions and surface finish to its structural integrity. This level of scrutiny is necessary because even a minor flaw can result in a major failure when the part is put into service.
Precision milling makes quality assurance easier by delivering parts that are already incredibly close to the desired specifications. With computer-controlled machines and advanced measurement tools, manufacturers can produce components with minimal variation. This means fewer errors, less rework, and ultimately, a higher-quality final product.
Why It’s Worth the Investment
Precision milling might seem like a costly and time-consuming step, but it’s an investment that pays off in the long run. For one, it reduces the likelihood of defects, which means fewer rejected parts and less wasted material. More importantly, it ensures that every component will perform as expected, reducing the risk of costly repairs or, worse, dangerous failures in the field.
In an industry where reliability is everything, investing in precision milling is a smart move. A well-milled part won’t just meet specs—it will exceed them, performing reliably over a long lifespan. That’s why so many aerospace companies rely on precision milling for their most critical components.